背景介紹 近年來,新興的反應數據采集、處理和控制技術已開始將制藥工藝開發轉化為日益豐富的科學數據領域。制藥企業開始采用 “工業4.0” 的方法,通過模擬在質量、安全、成本效益和可持續性方面,系統集成和大型數據分析是實現自動化和智能化的關鍵因素。充分利用這些技術進步進行工藝開發和過程在線控制可以顯著提高化學品生產的速度和可靠性。 制藥監管機構zui近推出了“質量源于設計”(QbD)計劃,鼓勵制造商在充分了解反應的基礎上設計和控制工藝。該計劃的關鍵是實時獲取化學工藝開發的數據,通過過程分析技術(PAT)進行過程監測。 制藥行業目前正在從活性藥物成分(API)的傳統的批量生產向連續加工轉變。FDAzui近的審查強調了PAT在連續流技術中的重要作用。PAT在連續流動系統中實現過程控制工藝優化,例如在實驗設計(DoE)中,通過自動化優化動力學模型和參數估計來指導藥物發現程序。 zui常用的實時在線PAT工具有UV/VIS、拉曼、紅外、和核磁共振。它們的使用變得越來越流行,部分原因是增加了商用臺式裝置。此外在連續流動平臺內可使用/超液相色譜(HPLC/UPLC)和GC等綜合色譜分析技術。 在學術和工廠實驗室內,離線分析技術仍然是司空見慣的。在這些情況下,樣品制備浪費時間,分析樣品并不總能表現當時反應性能。與僅使用離線分析的情況相比,使用實時分析的過程,數據將更快、更可靠的用于過程優化。 實例表明,目前在連續流程系統中集成單個在線分析儀器,用于分析一步反應已有很多良好的案例。而且,連續流化學的一個關鍵好處是能夠在不需要人工干預的情況下,在集成連續流系統內執行復雜的多級轉換,可以達到將不同的反應器模塊和分析方法結合到一個完整的一體化連續過程中。 歐洲連續流大咖的zui新成果 2019年4月08日,歐洲連續流專家C. Oliver Kappe教授研究小組的一項成果發表在Reaction Chemistry & Engineering期刊上(DOI: 10.1039 / C9RE 00087A )。該文章以在線分析與連續流化學相結合,構建了有利于工業4.0的未來實驗室如圖1b所示,并以化合物丙酸叔丁酯在該體系下合成β-羥基丁酸酯類產物為例進行了說明。如圖1a所示。 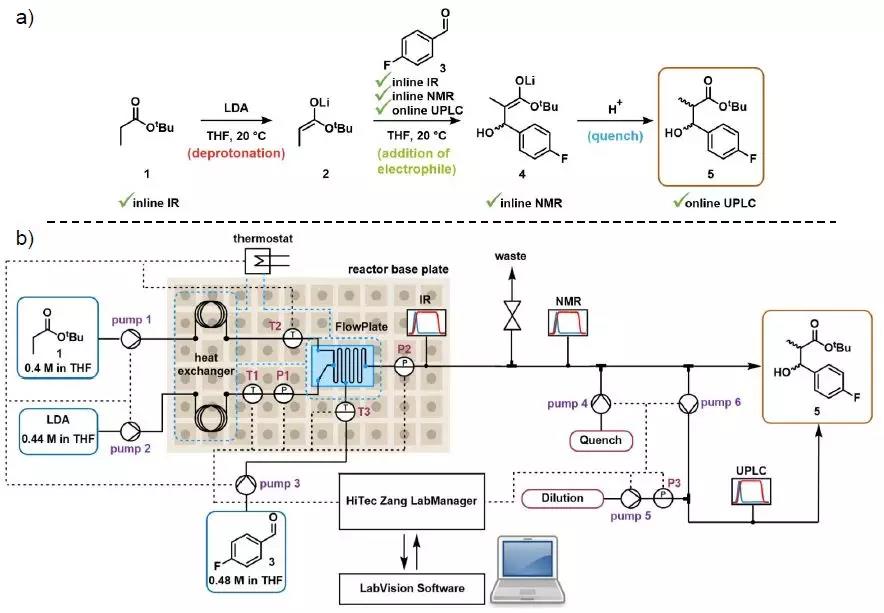 圖1. a)反應方案顯示丙酸叔丁酯1的去質子化,其與醛親電子試劑3的反應,然后驟冷,得到醛醇產物5;b)本研究中使用的zui終反應裝置示意圖,顯示泵,傳感器(T =溫度傳感器; P =壓力傳感器)和PAT儀器的位置,以及它們與LabVision控制系統的連接(黑色虛線=電信號連接線,藍色虛線=循環換熱介質路線)。 結果與討論: 步是通過用二異丙基氨基鋰(LDA)去質子化丙酸叔丁酯1來生成烯醇化物2(圖1a)。然后烯醇化物2與4-氟苯jia醛3反應生成金屬化的中間體4. 隨后用水原位淬滅得到所需產物5. 這類化學物質廣泛用于靶向合成相關藥物。 整個系統包括連續流反應器,四個進料泵,進料溶液包括: 1. 0.4M底物1和內標(聯苯)在THF中的溶液 2. 0.44M LDA在THF中的溶液 3. 0.48M 4-氟苯jia醛3在THF中的溶液, 4. 水 首先將基質1和LDA溶液混合以在1#反應片中形成烯醇化物2,停留時間為約5秒。隨后,將醛3溶液引入2#反應片中,在驟冷之前再反應80秒。驟冷的停留時間相當于約18秒。 將來自1#反應模塊的流出物通過IR流通池進行在線IR分析。然后使反應混合物通過在線流動池(0.8mL內部體積),用臺式NMR光譜儀(Spinsolve Ultra 43MHz,Magritek)監測。然后引入水以淬滅反應混合物并收集出口混合物。在引入水之后在線進行UPLC分析并通過對分餾的反應器輸出進行取樣來離線。在在線分析的情況下,將工藝流出的樣品轉移,然后用H2O / MeCN稀釋。 隨后,將6號通閥(2.6μL注射體積)注入等分試樣的稀釋流到LC柱上。連續流量設置中的泵和傳感器連接到HiTec Zang LabManager單元,并由LabVision軟件控制。 結果得到圖2,IR分析圖,圖3,NMR,圖4,UPLC分析圖,可以在反應的不同階段通過儀器實時監測反應及時觀察到過程的化學反應和生產。 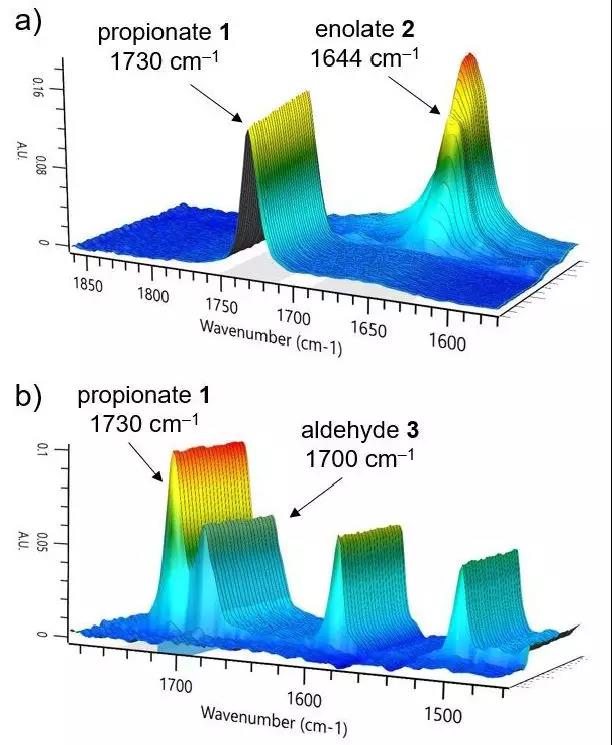 圖2. 代表性的ReactIR光譜 a)丙酸叔丁酯原料1及其去質子化形成烯醇化物2; b)丙酸叔丁酯1和醛親電子試劑3的組合溶液。 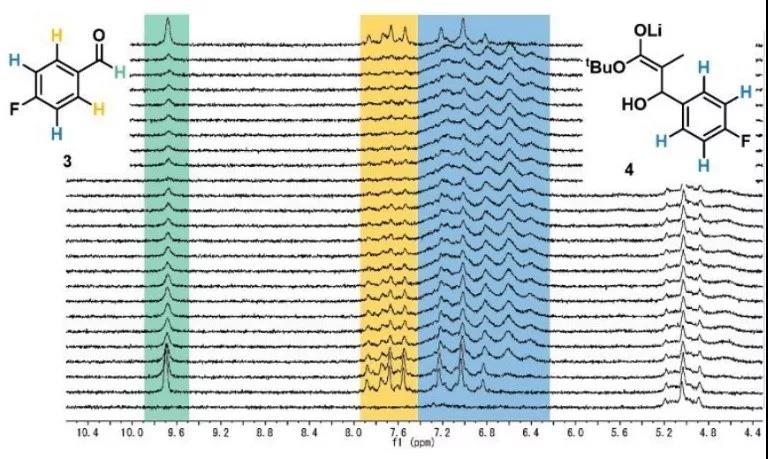 圖3. 反應混合物的堆疊NMR光譜 顯示醛3轉化為產物烯醇化物4的程度。使用配備有玻璃流通池的Magritek Spinsolve Ultra 43MHz獲得這些光譜。 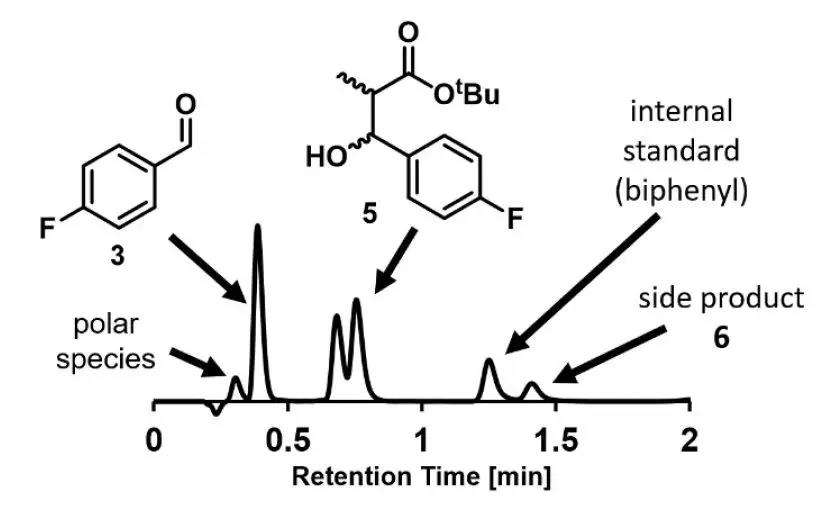 圖4. 代表性的UPLC色譜圖顯示了所有測量的反應組分 標記為“極性物質”的信號主要由4-氟苯甲酸組成,在醛3中作為次要雜質存在。并根據已有數據進行進一步分析得到圖5與圖6,對多步反應判斷更加準確。  圖5. 使用離線UPLC分析的實驗數據擬合的模型預測產品產量的等高線圖 ?
圖6. 橫向擴展運行的反應數據 a)總體反應方案,突出顯示量化的物種; b)圖表顯示了不同儀器檢測到的每個物種隨時間的數量。 在幾乎整個反應期間觀察到酯1的*去質子化,這意味著試劑遞送與任何流速變化的可忽略的影響一致(圖7b,紅線)。當觀察到兩次短暫的干擾時(29和32分鐘),酯1去質子化程度降低5%導致產率降低10%,持續約10分鐘。由這種微小偏差引起的這種顯著影響強調了該過程對微小變化的敏感性,以及實時反應監測的能力。 UPLC分析顯示在整個實驗期間所需產物5的產率為70-85%(圖6b,綠線),與來自先前產生的多項式模型的預測值相對應。然而,NMR監測提供了85-90%的前驅物4的始終較高的值。這種差異被認為是由于通過NMR在所需中間體4與副產物6之間的差的差異引起的。 這種副產物來自于將產物烯醇化物4加入到第二個親電試劑分子中(ESI第4.2節),并且其在整個反應過程中的增加與醛3的減少相對應。這突出了UPLC作為定量分析技術的能力,它在眾多化學物種之間的分辨率盡管值存在差異,但兩種技術觀察到的趨勢基本相同,從而進一步為獲得的數據提供了信心。 按比例縮小的連續流動過程在70分鐘的時間內成功運行,通過柱色譜法純化后分離出4.9g所需產物,相當于產率為70%,產率為4.2g h-1。 實驗結論 本研究已經證明了三種不同的在線分析儀器在模塊化反應器系統中的集成,可用于多步有機金屬反應的優化和過程監測。該模塊化流動反應器可通過多個傳感器和集成控制系統實現實時反應監測。 使用在線React IR監測LDA對丙酸叔丁酯1的去質子化,其中可以清楚地量化酯C = O拉伸的消失。隨后,使用醛質子和芳基質子作為不同的標記,通過在線NMR監測烯醇鋰加入到親電子試劑3中的進程。zui終的反應性能通過在線UPLC量化,通過定制的連續二次取樣稀釋系統實現。 利用大量數據快速探索反應參數,繪制實驗空間。對于生成的所有多項式模型,獲得了良好的擬合,允許估計每個參數的小變化將對總體反應性能產生的影響。使用集成傳感器和在線分析來監控每個反應步驟,從而擴大了流程。開發的具有集成PAT的反應器平臺支持數據豐富的實驗室環境,用于實時多步反應監測; 對于制藥和精細化工行業實現工業4.0以及未來實驗室至關重要。 |